Gas carburizing
Carburizing or Surface carbonation it refers to heat treatment in which the parts are surface hardened and at the same time, it has a relatively softer brain which are very resistant to mechanical stress and have high strength and toughness. In gas carburizing, carbon enters the furnace chamber by carrier gases which has constant pressure and atomic carbon diffiusion the surface of the part at a temperature above 900 degrees Celsius. In this way, a piece is made that its core is low in carbon and its surface is high in carbon.In the heat treatment unit of the Charkheshgar company, gas carburizing is carried out by two-shell furnaces of Aichiline.
Nitriding
Nitriding or nitrogenation is the same inserting atomic nitrogen in the surface layer of steel. In nitriding, the hardening agent is the formed metal nitride surface. Nitriding is done in the temperature range of 550 to 650. It should be noted that in this operation, there is no need for rapid cooling after heat treatment and the piece is cooled in the ambient air.
Carbonitriding
Carbon-nitrogenation is a surface hardening operation that in it, both nitrogen and carbon elements are absorbed on the surface and in this way, the absorbed nitrogen increases the hardness of the given carbon surface. The temperature range of carbonitriding is 800-875 degrees Celsius.
Hardening
When there is no need for carbon diffiusion in the surface hardness and only hardening is required in these cases, it is done by raising the temperature of the parts to the austenity range and then quenching which is done with a small potential of carbon or under nitrogen without the intervention of any other gas which is done in the heat treatment of Charkheshgar Co. by hot oils which has a temperature between 100 to 150 degrees Celsius and it prevents high dimensional changes as well as cracks.
Tempering
Due to the internal tensions created while cooling rapidly, all hardened pieces are somewhat brittle and brittle due to the return of internal tensions, they are reduced or deleted and therefore the impact strength is increased but instead, the hardness and strength of the hardened part will decrease to some extent.
Induction
Induction operation is the same local hardening that is used when there is no need to harden the whole part and only part of the part needs to be hardened in this case, the temperature is raised by induction devices by creating a magnetic field at the desired point and after heating up to the upper range of 800 quenching is done and hardening is done.
Pinning shot
After heat treatment, depending on the type of treatment the surface of the piece is usually cloudy or has an unacceptable smooth surface, which is polished by the shot pin of the surface of the parts by the grinding of the balls with a certain standard it also has a direct relationship with increasing the fatigue limit of parts.
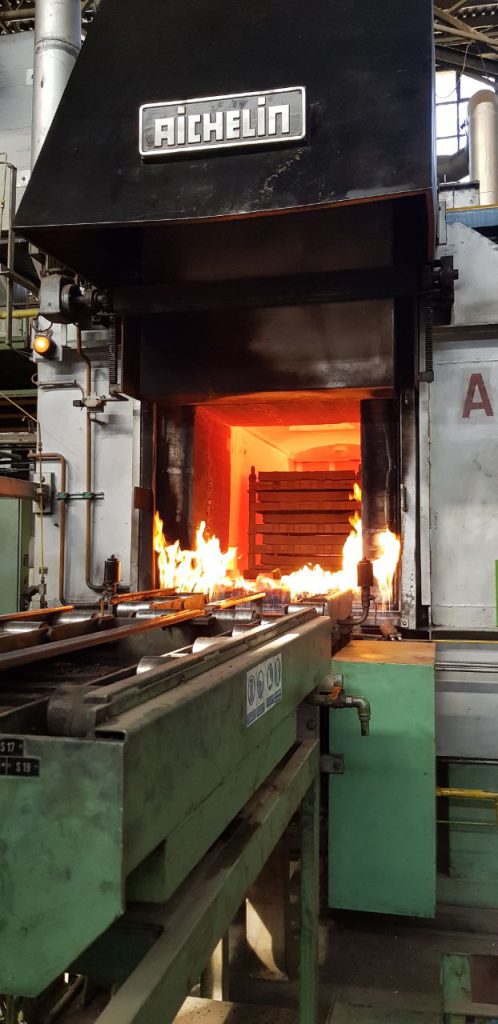